Time : April 18, 2023
Abstract: This article introduces the advantages of dynamic and static hybrid bearings, the steps and effects of using them for the transformation of connecting rod bearing shells.
Keywords: hybrid bearing of dynamic and static pressure; Connecting rod bearing bush boring machine; reform
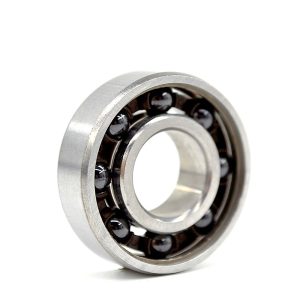
The KX-045 type connecting rod bearing bush boring machine used for precision machining of engine connecting rod bearing shells is a key equipment in the 6456 factory. The main component of this equipment, the boring head, is selected as a “C” level precision single row centripetal thrust ball bearing with the old number 46215, consisting of 4 groups in total. Due to the requirements of design accuracy, the boring head has very strict requirements for the selection and assembly of bearings. Even if the selection completely meets the requirements, the service life of the bearings is only 400 hours. Moreover, this type of bearing is expensive, and replacing a set of 4 bearings requires over 2000 yuan. The machine tool has 4 boring heads, and replacing 16 bearings simultaneously costs nearly 10000 yuan. Frequent replacement of boring head bearings has affected the normal operation of the entire factory production line.
After investigation and combined with our factory’s situation, if WMB liquid dynamic static hybrid bearings are used to modify the connecting rod bearing bush boring machine, only two of the four key heads can meet the usage requirements (the other two boring heads are used to process the auxiliary connecting rod bushing, and due to the small processing aperture and machine load, the rolling bearings can fully meet the requirements). The cost of renovating two boring heads is only about 40000 yuan, and the bearing technology is mature, reliable, and has a long service life.
Dynamic and static pressure bearings absorb the advantages of dynamic and static pressure sliding bearings and eliminate the disadvantages of both types of bearings. It adopts a surface shallow cavity oil wedge structure and utilizes the throttling principle of static pressure bearings to generate sufficient static pressure bearing capacity in the pressure oil chamber, allowing the main shaft to float when not rotating, thereby overcoming the dry friction caused by the start and stop of liquid dynamic pressure bearings, and improving the service life and accuracy retention of the main shaft and bearings. Moreover, due to natural surface throttling, Without the problem of clogging the throttle in the static pressure bearing, it is reliable to use. After the main shaft is started, the dynamic and static bearing capacity formed by the shallow cavity step effect greatly improves the bearing capacity of the main shaft, while the multi cavity opposed structure greatly increases the stiffness of the main shaft; The homogenization effect of high-pressure oil film and good anti vibration performance ensure that the spindle has high rotational accuracy and smooth operation. It has high stiffness, good vibration resistance, almost no friction and wear, and can maintain long-term usage accuracy. The bearing requires the lowest flow rate compared to others, has a simple structure, and is easy to replace.
The basic transformation steps are as follows:
- Grind the bearing seat hole of the boring head. After cleaning, use a grinding rod for rough and fine grinding, and the boring head should be placed in a vertical position for grinding. The required roughness of the bearing seat hole after grinding is Ra<0.32 μ m. Cylindricity 0.004mm.
- Determine the position of the oil circuit on the boring head body, and carry out drilling and tapping.
- Order bearings with a grinding allowance of 0.3-0.4mm based on the nominal size of the outer circle to ensure the necessary fit with the key body seat hole. After grinding, maintain a clearance of 0.006~0.008mm with the bearing seat hole. To ensure the coaxiality of the bearing outer circle and inner hole, it is required to install it on a mandrel with a taper of less than 1:10000 when grinding the bearing outer circle. When installing the bearing into the core rod, apply force and press it in. Do not use a blunt tool to smash it in to avoid bearing deformation and damage to the bearing hole. When taking out, hot water can be used to heat the bearing and expand it, which is both simple and safe. To facilitate the installation of the bearing into the bearing seat hole, the diameter of the first end of the bearing into the hole can be reduced by about 0.05mm, and the width can be tapered by about 10mm.
- After grinding the outer circle of the bearing, clean it strictly with clean kerosene or gasoline, and then install the bearing into the boring head hole. The distance between the end face of the bearing and the end face of the key body is about 5mm. When the bearing is installed too tightly, it should not be forcefully inserted. The following aspects should be checked: ① whether the bearing is installed correctly, ② whether the fit clearance is too small, and ③ whether there are dirt or burrs on the outer circle of the bearing and the boring head bearing hole.
- Install and clean the oil circuit system. After the bearing is installed, the oil circuit can be installed according to the information provided by the manufacturer. When cleaning the oil circuit, connect the supply and return pipes of the oil supply system, start the oil supply system, and carry out cyclic cleaning. Then connect the bearing oil circuit, restart the oil supply system to clean the entire bearing oil circuit system, and observe whether the oil injection into the oil inlet hole in the bearing is uniform and symmetrical, and promptly discover any problems with the oil circuit system.
- Equipped with grinding boring head spindle. To ensure that the original boring head spindle can still be used, the nominal size of the ordered bearing inner diameter is reduced by 0.2mm. The spindle is ground according to the bearing condition. Before grinding the spindle, the center hole should be polished to ensure that the spindle diameter and flange radial runout are within 0.003mm. The grinding size of the spindle and bearing should ensure a clearance of 0.028mm. After grinding, the cylindricity of the shaft diameter is ≤ 0.003mm, and the surface roughness Ra is ≤ 0.161μ m.
- Install the spindle. After cleaning the spindle, install it, drain the cleaning oil from the oil system and bearings, replace it with the specified lubricating oil, connect all oil circuits, release the overflow valve, and start the pump to run. Adjust the overflow valve to increase the oil supply pressure to 1.2 to 2.0 MPa. Check the oil chamber pressure of both bearings, which should generally be between 0.6 and 1.5 MPa. At this point, it is normal to rotate the spindle by hand and feel relaxed and free without any obstruction. It is best if the spindle can rotate itself during oil supply.
- Trial operation. After the installation of the bearing part, install the pulley and belt, adjust the belt tension (not too tight), and note that this work should be carried out when the oil supply system is turned on to avoid damage to the main shaft and shaft hole. Check if the oil supply pressure and bearing cavity pressure meet the requirements in item 7, and rotate the spindle to see if it is lightweight. If there are no abnormal situations, the spindle motor can be started to operate the spindle. At this time, the pressure in the bearing cavity will increase significantly due to the dynamic pressure effect, usually 2-3 times the pressure when the spindle is not rotating. After a trial run of 1 hour, the oil temperature tends to be basically constant. If there are no abnormalities, the boring tool bar can be installed for trial processing.
- Trial processing inspection. Conduct trial processing according to process requirements. After inspection, the roundness of the bearing hole decreased from 0.05mm to below 0.005mm, the cylindricity decreased from 0.01mm to below 0.005mm, and the surface roughness was lower than Ra0.16 μ m.
The modified connecting rod boring machine has shown good results after several years of operation.
- Improved the machining accuracy of the machine tool by one level.
- Reduced the surface roughness of the bearing bush machining by one level.
- Improved machine tool productivity and reduced annual downtime and repair hours by 60 hours. Reduce the processing time of a single connecting rod by half.
- The service life of the spindle and bearings has been extended, with an expected maintenance free period of nearly 10 years.
- It saves a large amount of bearing replacement and maintenance costs or the purchase cost of new machine tools, resulting in good economic results.
More about XBRG Self-aligning ball bearings:
Self-aligning ball bearings have two rows of balls, a common sphered raceway in the outer ring and two deep uninterrupted raceway grooves in the inner ring. They are available open or sealed. The bearings are insensitive to angular misalignment of the shaft relative to the housing , which can be caused, for example, by shaft deflection.
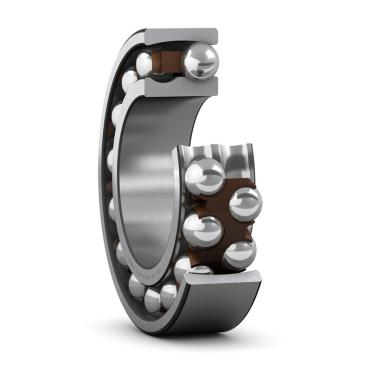